Orbital welding at RVS Non Ferro
At RVS Non Ferro, we understand that the quality and durability of weld joints are crucial for the efficiency and lifespan of installations. That’s why we specialize in orbital welding, an advanced welding technique known for its precision and repeatability.
Orbital welding is an automated process where the welding arc moves around the workpiece, usually a pipe. It is ideal for applications that require a consistent, high-quality weld. By using a welding machine that rotates the arc around the pipe, a highly uniform weld is achieved without the need for manual intervention.
Benefits of orbital welding
Excellent precision: Orbital welding delivers highly accurate and consistent welds, essential for piping in critical applications.
Repeatability: The automated process ensures reproducible results, enhancing the reliability of weld joints.
High quality: Controlled conditions result in high-quality welds with a reduced risk of defects and contamination.
Suitable for small diameters and thin walls: Orbital welding is ideal for applications where manual access is limited, such as small diameters or complex installations.
Time and cost efficiency: Automation improves weld quality and reduces production time, leading to lower costs.
Applications in machinery and complex weld assemblies
Orbital welding is widely used across various industries due to the demand for strong and precise weld joints. Our orbital welding services are ideal for:
Pipelines and tubes: Welding of pipelines and tubes in the oil and gas, chemical, and food industries, where leak-free and strong welds are crucial.
Pharmaceutical installations: Welding of sanitary pipes and pipelines where hygiene and precision are of utmost importance.
Aerospace: Application of orbital welding in the production of high-quality components for the aerospace industry.
Energy production: Welding of components for power plants and nuclear facilities, where reliable and durable connections are essential.
Orbital welding in the cleanroom
For applications requiring ultra-high purity, we offer orbital welding in a cleanroom environment. Cleanrooms maintain the highest levels of hygiene and contamination control, which is essential for industries such as semiconductors and pharmaceuticals. Our facilities are equipped to perform orbital welding in clean, controlled environments, ensuring weld joints that meet the strictest standards of purity and precision. This guarantees that your products remain free from contamination and are suitable for the most demanding applications.
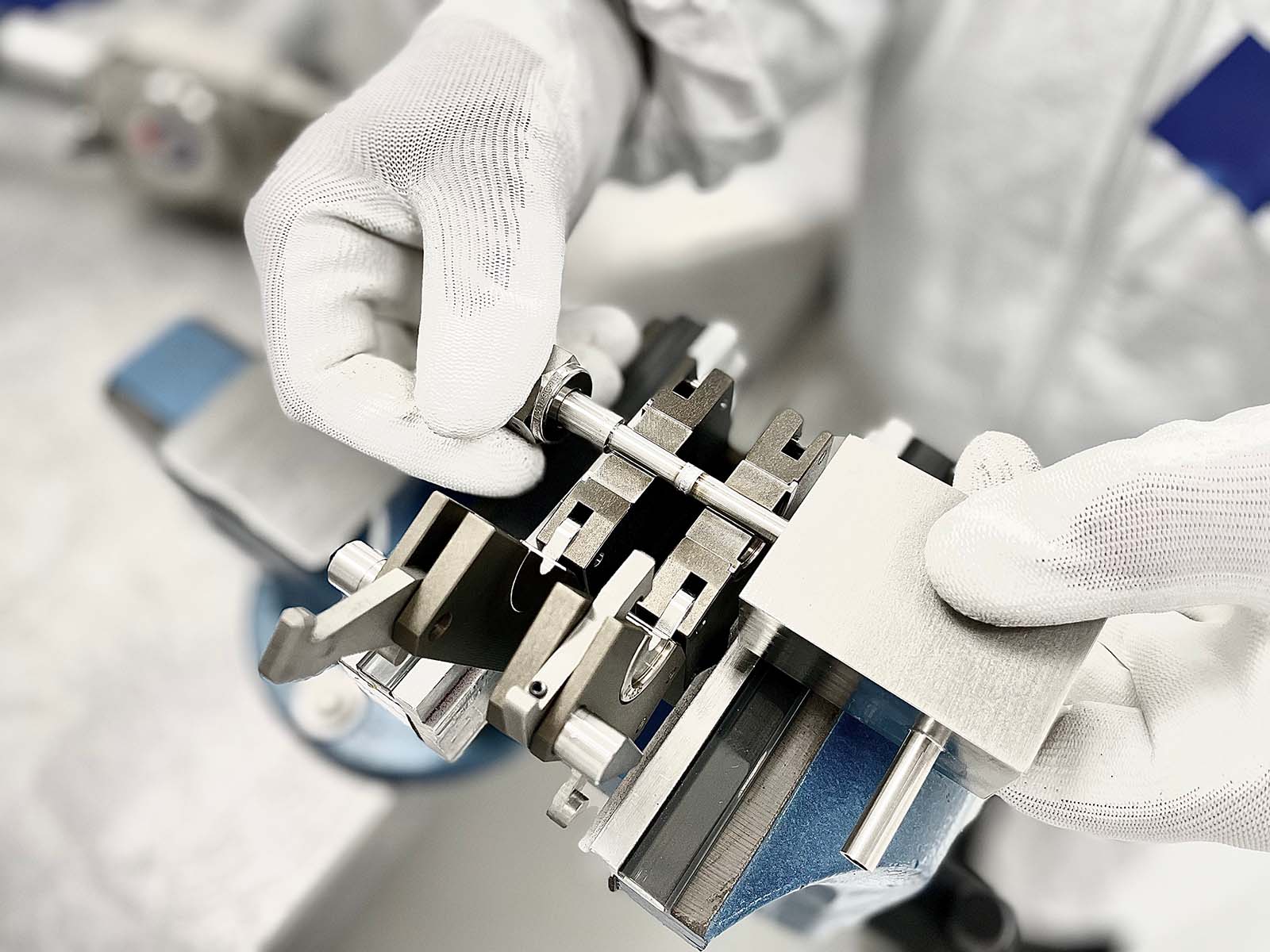
Our expertise
Quality comes first for us. Our team of certified welders and technicians has years of experience and operates advanced orbital welding equipment to complete your projects with the highest precision and efficiency. We understand the unique needs of critical industries and deliver welds that meet the highest standards.
Your partner in orbital welding
Are you looking for reliable and high-quality orbital welding solutions for your industrial projects? Contact us today for more information. Our team is ready to help you achieve your welding needs with the highest precision and quality.